- Home
- Additive Manufacturing
- Rapid Prototyping
Rapid Prototyping
Rapid prototyping and 3D printing. Two terms that are as firmly rooted together as steam engine and locomotive or offside and soccer. But why actually? Why are rapid prototyping manufacturing processes so closely related to 3D printing? Here you will get an overview.
What is Rapid Prototyping?
A definition: Rapid prototyping stands for the fast (rapid) production of prototypes. In other words, the rapid transfer of a product idea into an initial visual model for haptic, ergonomic, or functional testing. Prototypes are an essential part of all product development cycles and rapid product development processes and are particularly indispensable for preparing series products.
Rapid prototyping is about drastically shortening the prototyping manufacturing process in order to have the test model at hand as quickly as possible. The faster a prototype is available, the faster any optimizations and adjustments can be made that may be required to turn the prototype into a series product. 3D printing or additive manufacturing lends itself to the production of such prototypes, as it can be used to produce a corresponding prototype on demand – i.e. at the push of a button – based on a digital model.
Depending on the industry or application, additive manufacturing offers a wide variety of materials to produce the prototypes – be it metal, plastic, sand, or wax. After reviewing the test bodies, improvements can be made directly to the digital model, then a new prototype is 3D printed. In addition to rapid prototyping, there is also what is known as rapid tooling. This term stands for the rapid, additive manufacturing of a tool, for example for injection molding. Rapid manufacturing refers to the rapid production of usable components, such as spare parts.
Which processes fall under 3D rapid prototyping?
Essentially, generative, or additive manufacturing processes, also known as 3D printing, fall under rapid prototyping. This refers to all layer-based manufacturing processes in which various materials are joined together three-dimensionally layer by layer to produce a component. Of course, prototypes can also be produced using other technologies, such as milling.
Among the multitude of additive manufacturing technologies, rapid prototyping processes are considered the best known in the following overview:
Binder jetting technology compares well with the classic inkjet printing found in many homes and offices. In this process, a powder material such as sand or plastic is applied to a build platform. An industrial high-performance print head then moves over the build area and prints a complementary binder into the powder bed in those areas where the component is to be created. A layer of powder is then applied and bonded again. This process sequence is repeated until the desired component is completely printed and the unprinted material can be removed. Binder jetting is considered one of the most productive and scalable additive manufacturing processes.
Stereolithography is one of the oldest, patented additive manufacturing processes. It is based on a light-sensitive and liquid polymer that can be selectively cured using precise UV radiation. Unlike powder-based processes, a build area is lowered layer by layer into a bath filled with liquid photopolymer. With each layer, the build area is irradiated with a laser, which cures the plastic in the areas where the part is to be created. After printing is complete, the printed component is removed from the bath. Stereolithography is a very precise process that produces a particularly high and smooth surface finish.
In selective laser sintering (SLS for plastic materials) or selective laser melting (SLM for metal materials), a powder material such as plastic or metal is applied to a build area in a similar way to binder jetting. The build field is then controlled by a laser, which selectively sintered those areas of the material in which the desired component is to be produced. A new layer of material is then applied and sintered again by the laser. This process is repeated until the component is completely printed and can be unpacked. Very fine structures and components can be produced using SLS/SLM.
Fused Deposition Modeling (FDM) is a 3D printing process that is also used in most 3D printers for home use. In this process, so-called filaments, i.e. rolled-on plastic strings, are extruded through a heated nozzle. Much like a hot glue gun, the filament is printed through a nozzle that melts the material and deposits it on a build area. Depending on the CAD model, the component is thus placed “on top” of each other, layer by layer. The FDM process is one of the most cost-effective 3D printing processes and is particularly popular in the maker scene.
What are the advantages of rapid prototyping?
Rapid prototyping offers many advantages. We would like to emphasize and highlight three in particular at this point: Speed, cost, and materials.
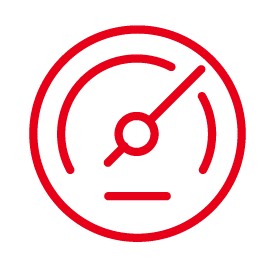
Speed
Since prototyping is primarily located in product development, the rapid production of prototypes made possible by 3D rapid prototyping pays off positively in terms of the time-to-market factor. The sooner a design or draft can be inspected, tested, and iterated as close to the original and as detailed as possible, the faster new products or product variations can be developed to market readiness and transferred to series production. This in turn opens up new sales opportunities and creates resources and capacities that flow into the faster generation of further products.
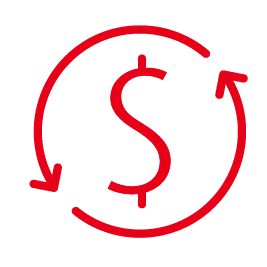
Costs
3D rapid prototyping printing offers considerable cost advantages, particularly due to the elimination of tooling. Producing your own tools for casting a component for various design iterations is risky. In case of doubt, they may never be used again because the design draft was discarded or declared to be undustable. Rapid prototyping can be used today to produce mock-ups quickly, precisely and without risk. This does not even require a rapid prototyping 3D printer of one's own, as there are now service providers and suppliers specializing in prototyping.
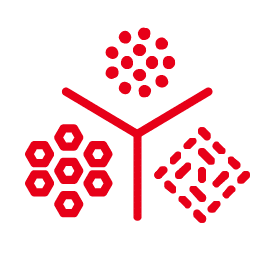
Material freedom
The portfolio of materials that can be processed, spread across all 3D printing technologies, is now enormous: from sands, ceramics, metals, and various plastics to organic tissue material. The areas of application for the development of prototypes are correspondingly broad. With rapid 3D printing, the geometric limits of the design are eliminated by the layer-by-layer structure. What can be printed is what is constructively conceivable. 3D rapid prototyping with its many advantages also facilitates design thinking: Existing components and products can be rethought - unprecedented things are created.
Which 3D printed parts can be produced with rapid prototyping?
The components that can be realized with 3D printing are similarly broadly positioned as the material portfolio. From technical components for industrial applications to mock-ups for consumer goods or the film and entertainment industry to architectural models, shoe soles for the sports and leisure sector or prostheses in medicine. One example of 3D rapid prototyping in the automotive industry would be engine components such as turbochargers.
Thanks to 3D printing additive manufacturing, rapid prototyping means several design iterations can be tested simultaneously, significantly shortening the optimization process and achieving an efficient result more quickly.
3D printing has long been firmly established in a wide variety of sectors and industries, and it is hard to imagine the development and production of prototypes without it.
How does voxeljet implement 3D rapid prototyping?
voxeljet has specialized in foundry applications for over 20 years. With our binder jetting technology, we process sands and plastics into molds and models for sand casting or investment casting. Especially when producing rapid prototypes for castings, 3D printing from voxeljet offers decisive cost advantages due to the above-mentioned savings in toolmaking. Foundries further process the 3D-printed molds and models to produce the corresponding casting prototypes. This 3D printing and rapid prototyping process can also be described as “rapid casting”, i.e. the rapid production of castings.
In addition, with our high-speed sintering technology, we also offer a process that can be used to produce functional prototypes from plastics such as PA12 or TPU. With our highly industrial 3D printers, prototypes of up to one meter component length can be produced in plastic and up to 4 meters in sand.
Which industries benefit from 3D rapid prototyping?
Across a wide range of industries, 3D rapid prototyping offers advantages. These include, in particular, the automotive, medical, and aerospace industries. Today, 3D printing and prototyping services are also widely used in the consumer goods industry. For product designers, architects and engineers, rapid prototyping has become an established tool for visualizing designs and producing test samples across industries.
FAQ
Rapid Prototyping
Rapid prototyping refers to the rapid production of prototypes, test specimens or mock-ups using additive manufacturing or 3D printing technologies. These prototypes are used for functional, haptic, or ergonomic testing during product development.
Industrial 3D Printing Systems
Our portfolio of industrial 3D printers ranges from compact systems for research to additive mass production.